Gyro Zeppeli Family: Delicious Greek Flavors For Everyone!
What are the key characteristics of a particular group of gyroscopic devices, and why are they significant in engineering and related fields?
This group of gyroscopic instruments, often employed in navigation and stabilization systems, share specific design attributes, materials, and operating principles. They are characterized by their ability to maintain a stable orientation or direction regardless of the movement of the platform they are mounted on. Examples include various inertial navigation systems and specialized stabilizers found in aircraft and spacecraft.
These gyroscopic devices hold substantial importance in numerous fields. Their ability to resist external forces, providing consistent readings, is crucial for applications requiring precise orientation and stability. Advancements in their construction have enabled increasingly sophisticated systems with enhanced accuracy and responsiveness. Their application has been critical in enabling progress in areas like aerospace, robotics, and even precision manufacturing, allowing for more stable and accurate movements and actions within those systems.
- Uncovering The Fortune Brenda Blethyns Net Worth Revealed
- Lucrative Earnings Unveiling The Salaries Of The Big Bang Theory Cast
This discussion will now delve into the specific designs, functionalities, and applications of this type of gyroscopic instruments, providing a broader understanding of their importance in modern engineering.
Gyro Zepelii Family
Understanding the "gyro zepelii family" necessitates exploring the core components and functionalities of gyroscopic devices, categorized by shared design principles. This examination highlights key aspects defining their operation and impact on various fields.
- Design
- Components
- Precision
- Stability
- Navigation
- Applications
- Instrumentation
- Accuracy
The "gyro zepelii family," encompassing various gyroscopic devices, emphasizes precision and stability through specific designs and components. These characteristics, combined with accurate instrumentation, directly impact navigation in aerospace. Applications range from aircraft stabilization to spacecraft orientation, showcasing the importance of precision within these systems. High accuracy and stability underpin navigation, critical for systems that require reliable measurements in dynamic environments. Design, components, and application-specific adaptations are key elements that collectively influence the performance of these instruments.
1. Design
The design of gyroscopic devices within the "gyro zepelii family" is intrinsically linked to their performance and applicability. Successful designs prioritize achieving precise rotational stabilization, critical for maintaining orientation in dynamic environments. This is accomplished through meticulous engineering of component interactions, including the rotor's geometry, bearing systems, and the overall structural integrity. Variations in design directly influence the sensitivity, response time, and accuracy of the gyroscope. For instance, advancements in materials and manufacturing techniques have led to more compact and robust gyroscopic units, enabling integration into smaller and more complex systems.
Practical applications demonstrate the significance of design. In inertial navigation systems, a precise design is crucial for accurately tracking movement and orientation. Similarly, in aircraft stabilization systems, the design ensures that the platform remains stable despite external forces. Different designs optimize the gyroscope for specific applications. A gyroscope designed for high-speed environments might emphasize rapid response time, whereas one employed in precision manufacturing might prioritize extreme stability. Effective design translates into reliable performance, a critical factor across numerous applications.
Understanding the interplay between design and performance within the "gyro zepelii family" is essential. Successful design translates into reliable operation, accuracy, and robustness. This knowledge informs engineering decisions in developing new systems and improving existing ones, ultimately leading to advancements in technology across fields like aerospace, robotics, and manufacturing. The critical relationship between form and function is central to the development and ongoing advancement of these devices.
2. Components
The "gyro zepelii family" is defined by the intricate interplay of its components. Each component, from the rotor assembly to the sensing mechanisms, contributes to the gyroscope's overall function. The rotor's precise design and material selection directly impact the device's stability and responsiveness. Sophisticated bearing systems, crucial for minimizing friction and maximizing precision, are another defining feature. Sensors, meticulously calibrated, translate rotational motion into usable data, enabling the system to maintain its orientation or direction. The interplay between these components dictates performance in diverse applications, ranging from inertial navigation systems to stabilization systems in aircraft.
Variations in components lead to variations in performance characteristics. For example, a high-precision gyroscope for spacecraft navigation will likely utilize advanced materials and extremely low-friction bearings to minimize errors. Conversely, a gyroscope designed for a consumer electronic device might prioritize cost-effectiveness and compactness, compromising somewhat on the level of precision. These choices in component selection influence the overall functionality and ultimately shape the application spectrum. The quality of components directly determines the system's capacity to maintain precise orientation and measurement in demanding environments. Real-world examples include advanced aircraft stabilization systems, where gyroscopic components are critical for maintaining flight stability, and precision manufacturing tools, where stable orientation is essential for accurate measurements.
Understanding the intricate relationship between components and performance is critical for engineering and design. Optimizing component choices enables the development of more accurate, efficient, and reliable gyroscopic systems. This understanding is essential to address challenges in maintaining stability and accuracy in dynamic environments, a crucial factor in many applications, particularly in aerospace and precision engineering. The "gyro zepelii family" embodies a complex interplay where the collective performance of components determines the overall utility of the device.
3. Precision
Precision is paramount within the "gyro zepelii family." The inherent nature of gyroscopic instruments necessitates extreme accuracy in their design and operation. Precise measurement of rotational motion is fundamental to their function. Deviations from precision directly impact the instrument's ability to maintain orientation or direction. This accuracy is crucial in applications requiring stable platform positioning, particularly in navigation and stabilization systems. Without precision, the instrument's output becomes unreliable, leading to errors in navigation, control, or measurement.
Real-world examples underscore the importance of precision. In aircraft, gyroscopes provide critical stabilization. Even small inaccuracies in the gyroscope's reading can lead to flight instability, posing safety risks. In spacecraft navigation, precision is essential for maintaining trajectory and achieving intended destinations. Subtle errors in gyroscopic readings can accumulate, potentially leading to significant deviations over long distances. Precision is equally vital in inertial measurement units (IMUs) used in robotics for accurate spatial awareness and movement control. Precise measurements are essential for the control algorithms to function reliably. Precise positioning and movement in applications like surgery and manufacturing are fundamentally linked to the precision of the underlying gyroscopic instruments.
The significance of precision within the "gyro zepelii family" extends beyond immediate applications. Understanding the intricacies of precision in these devices promotes the advancement of technology in various sectors. This knowledge fosters the development of more accurate and reliable instruments, leading to enhanced safety, efficiency, and precision in diverse fields. Furthermore, minimizing errors in gyroscopic measurements directly reduces costs and maximizes efficiency in numerous operations. The implications of this precision extend across industries, including aerospace, automotive, robotics, and manufacturing, emphasizing the fundamental role of accuracy in modern technological advancement.
4. Stability
Stability is a defining characteristic of gyroscopic devices within the "gyro zepelii family." The ability to maintain a consistent orientation or direction, regardless of external forces, is essential for their functionality in diverse applications. This inherent stability is achieved through specific design principles and mechanisms, influencing performance across various fields.
- Rotor Dynamics and Inertia
The rotor's mass distribution and angular momentum are critical for maintaining stability. Properly designed rotors resist external torques, preserving the device's orientation. High rotational inertia, a measure of resistance to changes in rotational motion, is a key design parameter. Examples include high-precision gyroscopes used in inertial navigation systems where consistent orientation is paramount for accurate positioning calculations. Without this robust stability, errors in readings would significantly impact applications requiring pinpoint accuracy. The performance of advanced stabilization systems for spacecraft or aircraft directly depends on the stability afforded by the rotor design.
- Bearing Systems and Friction Minimization
Efficient and low-friction bearing systems are essential for maintaining consistent rotational motion. Minimizing friction ensures that the rotor spins freely, with minimal resistance disrupting its equilibrium. This is vital for achieving the expected high accuracy and stability, particularly in devices that operate for extended periods. Precision bearings, often utilizing sophisticated materials and manufacturing techniques, contribute to the long-term stability of the entire system. Gyro-stabilized platforms in aircraft and spacecraft depend on the precision of these bearing systems for maintaining stable orientations even in turbulent environments.
- Environmental Factors and Compensation
External factors, such as vibrations and temperature fluctuations, can affect the stability of gyroscopic devices. Precise design considerations address potential impacts through damping mechanisms and temperature compensation systems. These features reduce the influence of outside factors on the internal stability of the system. This environmental resilience is vital in dynamic applications, such as gyroscopes used in automotive or marine navigation, where exposure to varying conditions is inherent to operation. Ensuring stability amidst changing conditions is crucial for the accuracy and reliability of measurements over time.
- Control Systems and Feedback Mechanisms
Control systems, often employing feedback loops, actively maintain stability. These systems constantly monitor the gyroscope's orientation and adjust parameters to counter any disturbances. Closed-loop control mechanisms dynamically adjust the gyroscope's rotation to maintain equilibrium, optimizing stability and accuracy. Applications like aircraft navigation and robotics extensively utilize gyroscopic systems with integrated control systems. The feedback mechanisms are essential for adapting to the continually changing environments and ensuring the device remains in its intended orientation.
The "gyro zepelii family" relies fundamentally on stability. Robust designs, meticulously chosen components, and sophisticated control strategies work in concert to create gyroscopic devices capable of withstanding external forces and providing precise orientation measurements. This characteristic stability, achieved through various techniques, is crucial for accurate functioning across a spectrum of technological applications. Improving stability translates directly into enhancing accuracy and reliability, making these devices crucial in diverse engineering sectors.
5. Navigation
The "gyro zepelii family," encompassing various gyroscopic devices, plays a pivotal role in modern navigation systems. Gyroscopic instruments are fundamental components, enabling precise directional measurements and maintaining stable reference frames in diverse environments. Their ability to resist external disturbances is critical for accurate navigation, particularly in dynamic conditions such as those encountered in aircraft, spacecraft, and marine vessels. The devices measure and quantify angular motion, forming the basis for accurate navigation calculations.
Real-world applications illustrate the significance of these devices. In aircraft navigation, gyroscopic instruments provide a stable reference frame for measuring and maintaining flight direction even in turbulent air. These devices are integral to inertial navigation systems (INS), calculating position and velocity independently of external signals. Similarly, in spacecraft navigation, gyroscopes are crucial for maintaining precise orientation during long journeys through space, essential for trajectory adjustments and precise maneuvering. Marine navigation also benefits from gyroscopic stabilization, contributing to accurate positioning and course maintenance. These practical applications demonstrate the profound impact of the "gyro zepelii family" on navigational accuracy and reliability.
The integration of gyroscopic instruments into navigation systems fundamentally alters the process. By providing a stable and accurate measure of angular velocity and orientation, these devices enhance the reliability of navigational data. This, in turn, improves the precision and efficiency of navigation systems. Understanding the principles governing the "gyro zepelii family" and their precise integration into navigation systems is vital for advancing these technologies, improving safety, and enhancing the capabilities of modern navigation systems in various demanding applications. The ongoing development of more compact, reliable, and high-precision gyroscopic devices promises even more accurate and efficient navigation systems in the future.
6. Applications
The "gyro zepelii family," encompassing various gyroscopic devices, finds broad application across diverse sectors. The inherent properties of these devices, particularly their stability and precision in measuring rotational motion, make them indispensable in a wide array of technological systems.
- Aerospace Navigation and Guidance
Gyroscopes are fundamental to inertial navigation systems in aircraft and spacecraft. Their ability to maintain a stable reference frame, independent of external disturbances, is crucial for accurate positioning and flight control. Complex calculations of trajectory, altitude, and heading rely on precise gyroscopic readings. This stability ensures accurate navigation, especially during long-duration flights or missions in challenging environments. In aerospace, the dependability of these instruments directly impacts safety and mission success.
- Robotics and Automation
Gyroscopic sensors are essential in robotic systems for precise movement control and orientation awareness. Accurate measurements of rotational motion allow robots to navigate complex environments, perform intricate tasks, and maintain stability during maneuvers. This precision is vital in applications ranging from industrial automation to surgical procedures and exploration robots. The ability to measure and react to angular changes empowers robots to operate reliably and efficiently.
- Automotive and Marine Navigation
Gyroscopes contribute to stability and directional awareness in vehicles. Automotive applications leverage gyroscopic sensors for anti-lock braking systems (ABS) and electronic stability control (ESC), enhancing safety and control. Similarly, marine navigation systems rely on gyroscopic instruments for precise heading and course maintenance. The inherent stability of these instruments makes them essential components in these systems, offering enhanced control and safety during challenging maneuvers.
- Precision Instrumentation and Manufacturing
In precise measurement and manufacturing processes, gyroscopic devices enable high-accuracy orientation and positioning control. These instruments are used in applications requiring highly precise measurements in sectors like semiconductor manufacturing, machine tool control, and metrology. Maintaining stable and controlled orientation is crucial for achieving required accuracy in these operations, guaranteeing high-quality products. The "gyro zepelii family" plays a significant role in ensuring precision and quality.
Across these sectors, the consistent and accurate measurement of rotational motion provided by the "gyro zepelii family" contributes significantly to system stability and overall performance. The increasing miniaturization and enhanced precision of these instruments continually expand their application areas, solidifying their vital role in modern technology.
7. Instrumentation
Instrumentation plays a fundamental role within the "gyro zepelii family." It encompasses the critical sensors, measuring devices, and associated systems that translate rotational motion into quantifiable data. Without precise instrumentation, a gyroscopic device loses its utility. The accuracy of the measurements directly impacts the overall performance and reliability of the system. Sophisticated sensors meticulously measure the minute changes in angular velocity, crucial for maintaining stability in navigation, control, and measurement applications. The chosen instrumentation directly determines the sensitivity, resolution, and error margins of the gyroscopic device. Examples include specialized accelerometers and gyroscopes incorporating sophisticated sensing mechanisms for enhanced data capture.
The interplay between instrumentation and performance is readily apparent across various applications. In inertial navigation systems (INS), precise instrumentation ensures accurate calculations of position and velocity, especially in dynamic environments where external forces are significant. Sophisticated gyroscopic instruments with advanced sensor technology are essential for achieving the high degree of accuracy demanded in aerospace and related fields. Similarly, in robotic systems, precise instrumentation in gyroscopes and associated sensors enables precise control of movement, leading to advanced automation capabilities. The reliability of instrumentation directly affects the robustness and accuracy of a robot's maneuvers. In many practical scenarios, the quality of the instrumentation directly influences the efficacy of the entire system. The precision of measurements is vital for safe and efficient operation across applications.
Understanding the intricate connection between instrumentation and gyroscopic devices is crucial for technological advancement. Selecting appropriate instrumentation directly affects the performance of the entire system. Improvements in sensor technology and data processing methodologies continually lead to more accurate and responsive gyroscopic devices, driving innovation in fields like aerospace and robotics. This understanding underpins the design and development of newer, more advanced instruments within the "gyro zepelii family." The consistent evolution in instrumentation directly impacts the capabilities and precision of these vital components, contributing to progress in various technical fields. The relationship between the two is not merely a technical connection; it is a critical factor in overall system reliability and accuracy.
8. Accuracy
Accuracy is a defining characteristic of the "gyro zepelii family." The precision of rotational measurements within these gyroscopic devices is critical for their function in diverse applications. Errors in measurement directly impact the reliability and effectiveness of systems utilizing these instruments. This facet examines the significance of accuracy in the context of these devices.
- Calibration and Error Minimization
Accurate gyroscopic measurements necessitate rigorous calibration procedures. Variations in the environment, such as temperature fluctuations, can introduce errors. Careful calibration and adjustments are essential to mitigate these errors. Specialized techniques and equipment are employed to ensure precise calibration. Examples include controlled laboratory environments and sophisticated sensor analysis tools to maintain accurate readings across diverse conditions. The reliability of the entire system hinges on the precision of calibration protocols.
- Material Selection and Manufacturing Processes
The choice of materials and the precision of manufacturing processes profoundly impact accuracy. Materials with stable physical properties and minimal susceptibility to distortions contribute significantly to the overall accuracy. Sophisticated manufacturing techniques, ensuring precise component tolerances and consistent geometries, are vital for minimizing errors. Accurate manufacturing directly translates to more accurate measurements in the gyroscopic device. For instance, advanced materials and machining methods are often employed for aerospace gyroscopes to withstand demanding environmental conditions while maintaining precision.
- Sensor Technology and Data Processing
Advancements in sensor technology directly correlate with improved accuracy. Modern gyroscopes utilize sophisticated sensors that are highly sensitive to subtle changes in rotational motion. Data processing algorithms also contribute to the reduction of measurement errors. Sophisticated signal processing techniques minimize noise and interference, thereby enhancing accuracy. Inertial navigation systems rely on high-accuracy gyroscopes with advanced sensor technology to provide accurate positioning information, essential in demanding environments.
- Environmental Factors and Compensation
Environmental factors, such as vibrations and temperature fluctuations, can influence the accuracy of gyroscopic measurements. Temperature compensation techniques, integrated into the design of the instruments, help maintain accuracy in various environments. Special design considerations, such as vibration isolation mounts, minimize external influences on the system's stability and precision. Instruments used in extreme environments, like spacecraft, require robust designs and sophisticated compensation methods to maintain high accuracy amid fluctuations. Accurate measurements under challenging conditions are often crucial for mission success and are directly linked to the stability of the instrument itself.
In summary, accuracy is not a singular aspect but rather an outcome of careful design choices throughout the "gyro zepelii family." From component selection and calibration procedures to the advanced sensor technologies and sophisticated data processing, each facet contributes to the overall precision of the instruments. Maintaining high accuracy across various applications and environmental conditions is paramount for the reliability and effectiveness of these gyroscopic devices in diverse engineering applications.
Frequently Asked Questions about the Gyro Zepelii Family
This section addresses common inquiries regarding the "gyro zepelii family," a group of gyroscopic instruments crucial in various applications. The following questions and answers aim to provide clarity and understanding.
Question 1: What distinguishes the gyro zepelii family from other gyroscopic devices?
Specific design attributes, materials, and operating principles differentiate devices within this group. Key features include shared methodologies for precise rotational stabilization, ensuring consistent orientation regardless of external forces acting on the platform.
Question 2: What are the primary applications of devices within this family?
These devices are integral components in inertial navigation systems, particularly in aerospace and robotics. Their use extends to stabilization systems for vehicles and precision instrumentation in demanding manufacturing environments.
Question 3: How does the accuracy of these devices compare to other types?
Accuracy is paramount in the "gyro zepelii family." Thorough calibration, advanced materials, and sophisticated manufacturing processes contribute to highly precise rotational measurements. Maintaining consistent accuracy in dynamic conditions is crucial.
Question 4: What factors influence the stability of these gyroscopic devices?
Stability stems from the design of the rotor, the minimization of friction within bearing systems, and effective control systems. These components work in concert to resist external forces, maintaining a consistent orientation.
Question 5: How does the design impact the performance of gyro zepelii family devices?
Specific designs prioritize rotational stabilization and material selection. Variations in design directly influence a gyroscope's sensitivity, response time, and overall accuracy. The intended application greatly shapes the device's specific design.
Understanding these aspects clarifies the crucial role of the "gyro zepelii family" in modern technology, highlighting their accuracy, stability, and adaptability across diverse fields.
The next section delves deeper into the specific designs, functionalities, and applications of various members within this family.
Conclusion
The "gyro zepelii family" encompasses a diverse range of gyroscopic instruments characterized by their precision in measuring rotational motion. This exploration highlighted the critical role of design, components, stability, and accuracy within these devices. Their stability, achieved through precise rotor dynamics and low-friction bearings, is essential for maintaining consistent orientation in dynamic environments. The devices' ability to resist external disturbances is crucial for applications demanding accurate directional awareness. The instruments' accuracy, stemming from rigorous calibration, advanced materials, and sophisticated sensor technologies, is vital for reliable measurements. This analysis underscores the fundamental importance of these devices in various fields, including aerospace navigation, robotics, and precision manufacturing. The ongoing development and refinement of these gyroscopic instruments promise further advancements in technology.
The "gyro zepelii family" stands as a testament to the power of precise engineering and sophisticated instrumentation. The continued evolution of these devices hinges on advancements in materials science, sensor technology, and data processing techniques. Future research into these aspects will undoubtedly yield even more accurate and adaptable gyroscopic instruments, driving progress in numerous technological domains. The significance of this family of gyroscopic devices extends beyond present applications, promising even more sophisticated and reliable systems in the future.
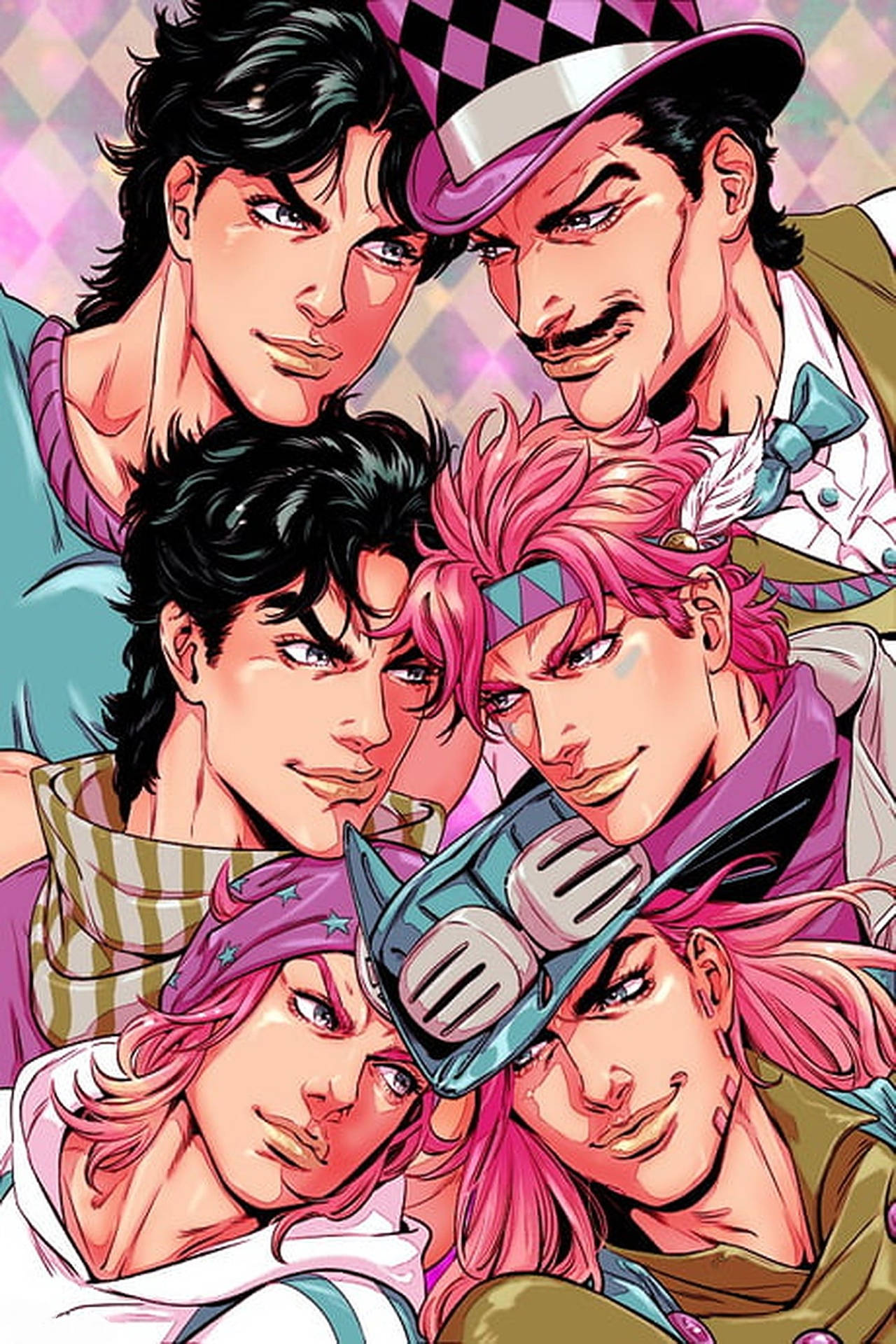
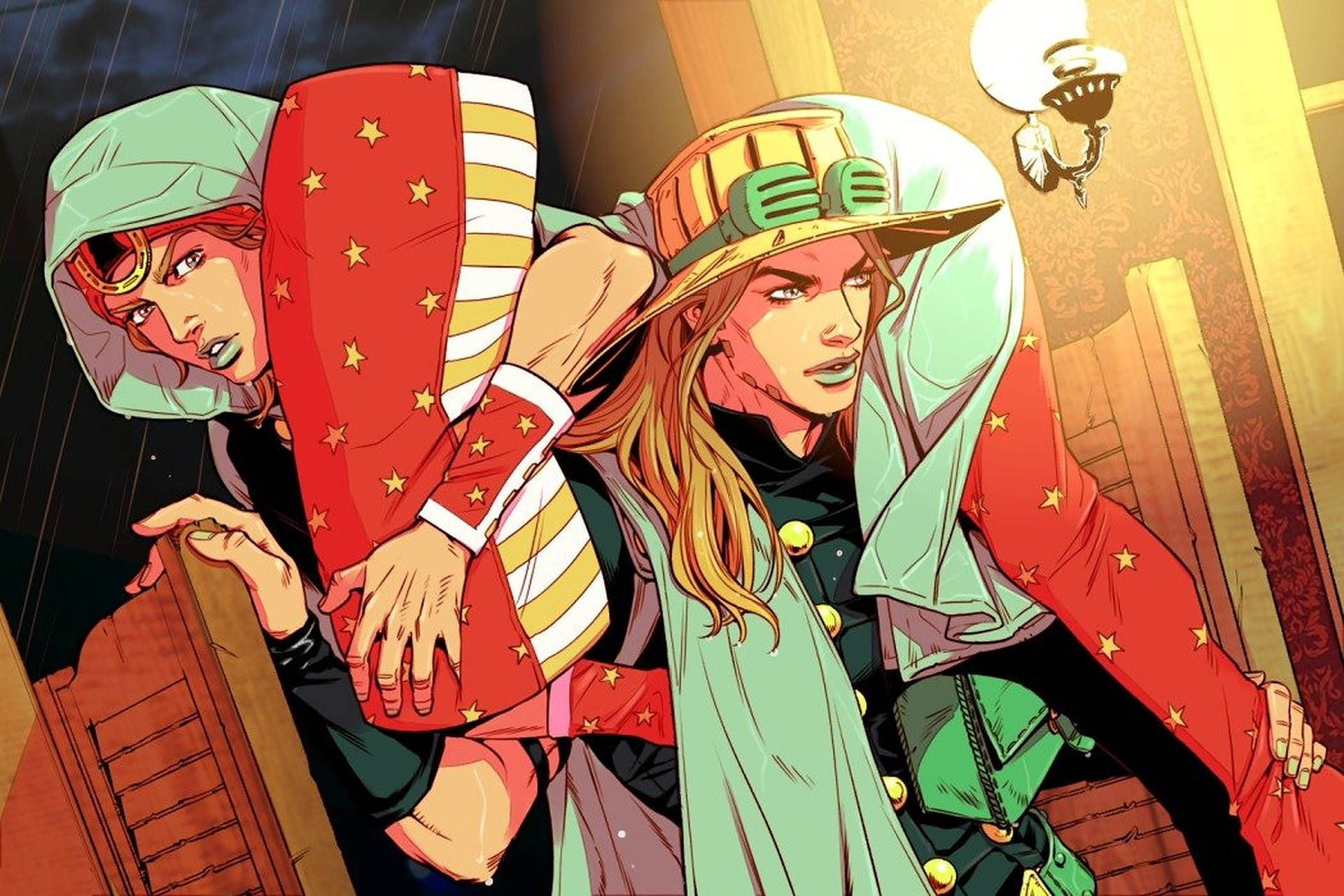

Detail Author:
- Name : Prof. Maybelle Kunde DVM
- Username : stokes.etha
- Email : hannah53@hotmail.com
- Birthdate : 1997-07-20
- Address : 1754 Aniya Well New Clementina, MO 79255-1451
- Phone : 1-364-967-7868
- Company : Connelly, Rolfson and Corwin
- Job : Private Detective and Investigator
- Bio : Consequatur aut repudiandae beatae. Cupiditate voluptatibus eos dolore modi. Aut consequuntur qui eius blanditiis vel provident maiores.
Socials
facebook:
- url : https://facebook.com/keely1022
- username : keely1022
- bio : Officia ipsam sit error ipsa deserunt magnam quod.
- followers : 5492
- following : 278
instagram:
- url : https://instagram.com/lockman1997
- username : lockman1997
- bio : Voluptas ipsa sunt totam et. Et laboriosam ut laudantium nesciunt.
- followers : 3474
- following : 1306
twitter:
- url : https://twitter.com/lockmank
- username : lockmank
- bio : Voluptatibus consequatur sapiente aspernatur tempora autem. Suscipit qui et ut ex. Adipisci quo id voluptas provident similique.
- followers : 4235
- following : 1904
linkedin:
- url : https://linkedin.com/in/keely_lockman
- username : keely_lockman
- bio : Quidem accusantium ducimus sed est dolorem.
- followers : 6175
- following : 14