Jackerman 3D: Stunning 3D Models & Designs
What are the implications of this innovative 3D modeling technique? A comprehensive approach to 3D modeling offers significant advantages for various applications.
This advanced 3D modeling methodology, a sophisticated approach to generating 3D representations, encompasses a range of techniques. It likely involves sophisticated algorithms and software to produce high-fidelity 3D models. Examples could include 3D visualizations of complex mechanical systems, architectural designs, or intricate biological structures. The specific methods employed and the resulting outputs would depend on the intended application.
The benefits of such a 3D modeling approach are manifold. Improved accuracy in designs, enabling more precise simulations, is key. Enhanced visualization capabilities allow for a better understanding of complex data and structures. This can lead to significant improvements in design efficiency, product development cycles, and ultimately, better outcomes. Further, the approach might have applications in scientific research, enabling detailed analysis and visualization of data in fields like medicine and engineering.
- Exclusive And Spicy Sophie Rain Nsfw Image Gallery
- Sydney Smiths Substantial Net Worth A Detailed Examination
Further exploration is needed to determine the exact characteristics, uses, and benefits of this 3D modeling process in various applications. Details about specific applications, historical context, or associated individuals could provide a deeper understanding. This exploration will allow us to determine the significance of this technique.
Jackerman 3D
Understanding Jackerman 3D necessitates examination of its core components. These crucial elements contribute to its overall efficacy and impact. Analysis of these aspects provides a comprehensive understanding.
- Modeling techniques
- Software applications
- Data input methods
- Output formats
- Accuracy standards
- Validation procedures
Jackerman 3D, as a sophisticated 3D modeling process, likely relies on advanced modeling techniques. Software applications are essential for implementation. Data input methods affect the quality of the resultant 3D model. The output formats are crucial for the downstream processes. Established accuracy standards ensure reliability. Robust validation procedures guarantee the reliability and correctness of the results. For instance, high-accuracy 3D models are vital in fields such as architecture, engineering, and medicine to assure accurate visualizations and simulations.
- Get Organized With Grand Piece Online Trello Your Ultimate Trello Guide
- Comprehensive Directory Of Female Cartoon Character Names From A To Z
1. Modeling Techniques
The effectiveness of "Jackerman 3D," whatever its precise methodology, hinges critically on the employed modeling techniques. These techniques determine the accuracy, detail, and ultimately, the usefulness of the resultant 3D models. Sophisticated techniques, capable of handling complex geometries and data sets, are essential for producing high-quality models applicable in various fields. For example, in architectural design, precise 3D models allow for accurate structural analysis and visualization of the completed building, facilitating early identification and resolution of potential issues. Similarly, in engineering, detailed 3D models of mechanical systems enable simulations of performance, facilitating design optimization and problem-solving.
Specific modeling techniques employed within "Jackerman 3D" likely encompass a range of approaches, including polygon modeling, NURBS modeling, or mesh-based techniques. The choice of technique influences the model's characteristics. Polygon modeling, for example, lends itself to more straightforward representation of simple objects but may struggle with complex shapes and curves. NURBS modeling provides greater flexibility for complex shapes and curves but may require specialized software and skills to execute effectively. The specific techniques used determine the level of detail and accuracy attainable in the final 3D model. This is vital because the fidelity of the model directly impacts downstream analyses and applications.
Understanding the modeling techniques underpinning "Jackerman 3D" is crucial. The proper technique enables the generation of accurate and reliable 3D models. This, in turn, leads to a more efficient and effective approach to design, analysis, and problem-solving in diverse fields. The choice and application of modeling techniques are fundamental elements in the overall process and ultimately dictate the success of the method's application.
2. Software Applications
Specific software applications are integral to the implementation and operation of "Jackerman 3D." The effectiveness of the 3D modeling process is directly tied to the capabilities and features of the software used. Appropriate software must support the chosen modeling techniques, data input methods, and desired output formats. Failure to select suitable software can significantly impede the entire process.
- Modeling Capabilities
The chosen software must possess the necessary tools to implement the core modeling techniques underlying "Jackerman 3D." This includes functionalities for creating, manipulating, and modifying 3D shapes, surfaces, and objects. Examples might include tools for polygon modeling, NURBS curves and surfaces, mesh editing, or parametric modeling, depending on the specific modeling approach. The software's capacity to handle complex geometries and large datasets is paramount for applications demanding intricate detail.
- Data Input and Output
The software must seamlessly integrate with data input sources, potentially including CAD files, 2D images, or 3D scans. Importantly, the software should facilitate the export of 3D models into compatible formats for further analysis, visualization, or integration within other systems. Examples may include exporting data as STL files, OBJ files, or specialized proprietary formats. This interoperability is vital for streamlined workflows and downstream utilization of the 3D models.
- Visualization and Simulation Tools
Software for "Jackerman 3D" should provide robust visualization tools to inspect and analyze the models created. This may involve features for rendering images, creating animations, or facilitating simulations. Examples could encompass advanced rendering engines and tools for analyzing stress, strain, or other properties of the modeled objects. These visualization and simulation capabilities are crucial for understanding, interpreting, and utilizing the generated 3D models.
In conclusion, the proper selection and utilization of software applications are critical components of the "Jackerman 3D" process. The modeling capabilities, data management, and visualization tools provided within the chosen software are directly correlated to the quality and usability of the final 3D representations. The selection process must consider the particular needs of the applications to ensure efficient and effective results.
3. Data input methods
The efficacy of "Jackerman 3D" is intrinsically linked to the quality and appropriateness of data input methods. Accurate and complete data input is fundamental to generating reliable 3D models. Imperfect data directly translates to inaccuracies in the final product. A critical understanding of these input methods is essential for successful application in diverse fields. For example, in architectural design, imprecise measurements or inaccurate scans of existing structures can lead to flawed 3D models, hindering the accuracy of structural analysis and potentially causing costly errors during construction. Similarly, in engineering, faulty input data from sensors or simulations can produce unrealistic 3D models of machine components, leading to flawed performance predictions and inefficient designs.
Various methods for data input could be employed in "Jackerman 3D," each with its own limitations and advantages. These methods include direct measurements, digital scans from various technologies (laser scanning, photogrammetry), and data import from existing CAD (computer-aided design) files. The choice of method is crucial and depends on the specific application. Direct measurements, although precise when performed meticulously, are time-consuming and impractical for large-scale or complex projects. Digital scans, such as laser scanning, provide efficient data acquisition for complex geometries but require specialized equipment and expertise. Import of existing CAD files can be convenient but depends on the format's compatibility and potential limitations of the original data. The data input methods chosen must align with the desired level of detail, accuracy, and efficiency for the intended outcome. The appropriate selection of these methods ultimately contributes to the overall quality and reliability of the "Jackerman 3D" process.
In summary, meticulous consideration of data input methods is paramount for the success of "Jackerman 3D." The selection of appropriate methods, considering factors like precision requirements, project scale, and available resources, is crucial for producing accurate and reliable 3D models. Failure to acknowledge the importance of data integrity and methodological appropriateness can lead to significant errors and undermine the value of the modeling process. Addressing the challenges associated with each data input method and choosing the most suitable options is essential to optimize the entire "Jackerman 3D" workflow and ensure practical application across diverse fields.
4. Output formats
The suitability of output formats significantly influences the utility and impact of "Jackerman 3D." The choice of file format directly affects the subsequent steps in the process, including downstream analysis, visualization, and integration with other systems. A critical understanding of these formats is essential for maximizing the value generated by "Jackerman 3D." For instance, exporting a 3D model of a complex mechanical component as a highly compressed format might lead to loss of critical details, rendering the data unsuitable for precise engineering analysis. Conversely, selecting a format that preserves full geometric detail allows for accurate simulations and detailed visualizations. This selection process ensures that the model retains its fidelity and allows for future manipulation without significant loss of information.
Specific output formats employed by "Jackerman 3D" will determine the level of detail preserved. Formats like STL (stereolithography), OBJ (Wavefront OBJ), or 3MF (3D Manufacturing Format) each have strengths and weaknesses, each influencing downstream usage. STL files, commonly used in 3D printing, primarily store surface geometry and lack internal representations. OBJ files, while often compatible with many 3D modeling programs, do not necessarily preserve full semantic data. 3MF, a relatively newer standard, aims to address some of the limitations of the previous formats by including more contextual information, improving interoperability and usability for manufacturing applications. This suggests an understanding of the target application is critical, as the most suitable format can vary greatly from one project to another. Selection of an appropriate output format is pivotal for ensuring seamless integration and successful utilization in various fields, such as engineering, medicine, or design.
Ultimately, the connection between output formats and "Jackerman 3D" underscores the importance of considering downstream applications. Choosing the correct format, depending on the specific needs of the subsequent analysis or manufacturing process, is vital. The selection process should prioritize preserving data integrity and ensuring compatibility with relevant software and hardware. Careless selection of output formats can impede data usage and cause delays or errors. Therefore, a robust understanding of the specific needs of the project and the characteristics of various output formats is crucial for optimizing the "Jackerman 3D" process and maximizing its value in diverse applications. This understanding directly contributes to a successful and productive workflow.
5. Accuracy Standards
Accuracy standards are critical to the reliability and value of "Jackerman 3D." The precision and fidelity of the 3D models generated directly depend on adherence to established standards. These standards ensure consistency, comparability, and the trustworthiness of the outputs across diverse applications. Deviation from these standards can lead to significant errors and undermine the credibility of the results.
- Geometric Accuracy
Geometric accuracy standards dictate the permissible deviations from ideal shapes and dimensions. This is crucial for representing objects with precise details. For instance, in architectural design, minute discrepancies in wall thicknesses or window placements can lead to significant errors in structural analysis and potentially compromised safety. Similarly, in engineering, inaccuracies in mechanical part dimensions can compromise functionality and safety. Violation of these standards in "Jackerman 3D" could result in flawed designs and simulations, leading to costly rework or safety concerns.
- Dimensional Accuracy
Dimensional accuracy standards define the permitted tolerance levels for measurements. These standards specify the precision required in measuring and representing objects' sizes and distances. In industrial manufacturing, slight variations in component dimensions can result in parts not fitting together correctly or functioning as intended. Similarly, in medical imaging, precise measurements are essential to accurately represent anatomical structures. Failure to meet these standards in "Jackerman 3D" compromises the precision of models and the reliability of subsequent analyses.
- Data Representation Accuracy
Standards for data representation accuracy specify how to present and store the data related to "Jackerman 3D" models. This ensures consistency and allows for seamless integration with other systems. For example, inconsistency in the representation of material properties or physical constraints could lead to misinterpretations of simulations and predictions. Violation of data representation standards in "Jackerman 3D" would hinder the interpretation, analysis, and application of the models, potentially affecting the reliability of conclusions based on these models.
- Validation and Verification Procedures
Establishing and adhering to rigorous validation and verification procedures are crucial for ensuring the accuracy of "Jackerman 3D" models. This includes steps for confirming that the models accurately reflect the intended subject and the accuracy of the data used to generate them. For example, independent verification of model parameters is essential to ensure their accuracy. Appropriate validation procedures ensure the model's accuracy and reliability. The absence of these procedures in "Jackerman 3D" could lead to significant errors in model representation and downstream applications.
In conclusion, adhering to well-defined accuracy standards is paramount for "Jackerman 3D" to provide dependable results. These standards govern every facet of the process, from geometric representation to data handling, ultimately assuring the integrity, reliability, and utility of the generated 3D models. Failing to meet these standards jeopardizes the process's credibility and applicability across diverse applications.
6. Validation Procedures
Validation procedures are indispensable components of any robust 3D modeling process, including "Jackerman 3D." Their purpose is to ascertain the accuracy and reliability of the generated models. These procedures ensure that the models faithfully represent the intended subject and data, minimizing potential errors and inaccuracies. Failure to implement rigorous validation can compromise the models' utility in downstream applications, from design and engineering to scientific research.
- Comparison with Reference Data
A fundamental validation step involves comparing the output of "Jackerman 3D" with existing, trusted data. This reference data can originate from physical measurements, established CAD models, or validated simulations. Discrepancies between the "Jackerman 3D" model and the reference data highlight potential errors within the modeling process. For example, in architectural design, comparing the 3D model of a building with surveyed blueprints can identify inaccuracies in dimensions or spatial relationships. Within "Jackerman 3D," this comparison would ensure the accuracy of generated geometries.
- Independent Verification of Input Data
Validating the input data is paramount. Errors in the initial data directly impact the model's accuracy. Reviewing the accuracy of data points, scans, or measured values is essential. For instance, an engineering application might validate sensor data used to generate a 3D model of a machine component, checking for anomalies or errors in the collected readings. This step ensures that "Jackerman 3D" does not propagate inaccuracies present in the input data.
- Model Simulation and Analysis
Simulating the modeled object or system under various conditions provides further validation. This step involves testing the "Jackerman 3D" output using established simulation tools and comparing the outcomes with expected results. In engineering, simulations can verify the structural integrity of a bridge design by applying simulated loads. Applying comparable simulations and analyses to "Jackerman 3D" models allows for comprehensive testing and validation.
- Iterative Refinement and Adjustment
Validation procedures often involve an iterative process. Discrepancies or anomalies identified during validation necessitate modifications to the "Jackerman 3D" process. This might involve adjusting input parameters, optimizing algorithms, or refining the modeling techniques. This iterative approach ensures that the process produces progressively more accurate and reliable models. This refinement process can apply to several steps within "Jackerman 3D," from data input to output format.
In essence, rigorous validation procedures are crucial for the trustworthiness and usability of "Jackerman 3D" models. The meticulous application of comparison, independent verification, simulation, and iterative refinement significantly strengthens the reliability of the output, ensuring models accurately reflect reality and can be confidently used in diverse applications. The quality of the generated 3D models relies heavily on the thoroughness and appropriateness of these procedures.
Frequently Asked Questions about "Jackerman 3D"
This section addresses common inquiries regarding "Jackerman 3D," a 3D modeling methodology. Clarity on these points is essential for a thorough understanding of the process and its applications.
Question 1: What are the core components of "Jackerman 3D"?
The process encompasses several critical elements, including specific modeling techniques, software applications, data input methods, output formats, accuracy standards, and rigorous validation procedures. These components interact to generate high-quality 3D models.
Question 2: What software applications are typically used with "Jackerman 3D"?
Specific software choices depend on the chosen modeling techniques, but applications capable of handling complex geometries, supporting various data input formats, and producing high-fidelity output are necessary. Compatibility with CAD formats and efficient visualization tools are further requirements.
Question 3: What input methods are compatible with "Jackerman 3D"?
Input methods vary depending on the application. Potential methods include direct measurements, digital scans (laser scanning, photogrammetry), or the import of existing CAD data. The most suitable method depends on the complexity and scale of the project and desired level of accuracy.
Question 4: How does "Jackerman 3D" ensure accuracy?
Accuracy is paramount. The process adheres to established geometric and dimensional standards. Furthermore, rigorous validation procedures, including comparison with reference data, independent verification of input, and model simulation and analysis, are employed to ensure accuracy. Iterative refinement further strengthens accuracy.
Question 5: What are the typical output formats of "Jackerman 3D"?
Typical output formats depend on the intended application. Commonly used formats include STL, OBJ, and 3MF. The selection of an appropriate output format is critical for compatibility with downstream processes, ensuring the integrity of the model's data and facilitating its use in subsequent analyses or manufacturing processes.
Understanding these aspects of "Jackerman 3D" provides a foundation for evaluating its suitability for various applications.
This concludes the FAQ section. The following sections delve deeper into the practical aspects of employing "Jackerman 3D" in specific applications.
Conclusion
"Jackerman 3D," as a 3D modeling methodology, presents a complex interplay of technical components. The success of this approach hinges on the careful selection and integration of modeling techniques, software applications, data input methods, and output formats. Accuracy standards and rigorous validation procedures are essential to ensure the reliability and trustworthiness of the resultant 3D models. The process necessitates a deep understanding of the interdependencies between these elements and the specific requirements of the intended application. Failure to address these interdependencies can lead to inaccuracies, flawed designs, and ultimately, reduced value in various fields. The method offers potential advantages in terms of precision and efficiency but demands careful planning and execution. The analysis of the methodology highlights the need for expertise in both modeling techniques and the software applications employed.
Future research should explore optimization strategies and potential enhancements to the "Jackerman 3D" methodology. Investigating how it can effectively address challenges in specific fields, such as engineering design or scientific visualization, is warranted. The careful examination and application of this methodology will undoubtedly influence and shape future design processes, emphasizing the critical nature of accuracy in 3D modeling techniques.
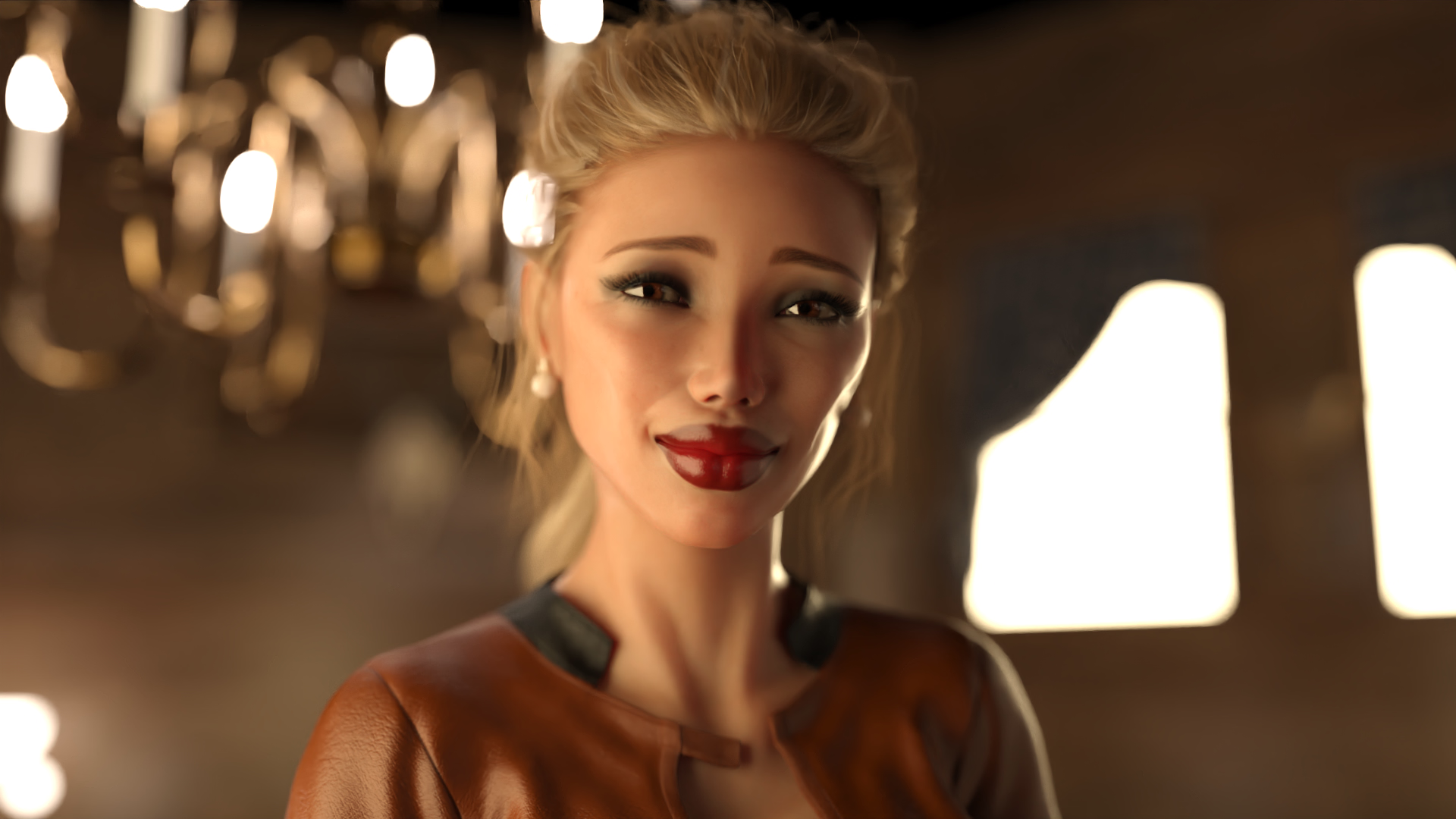
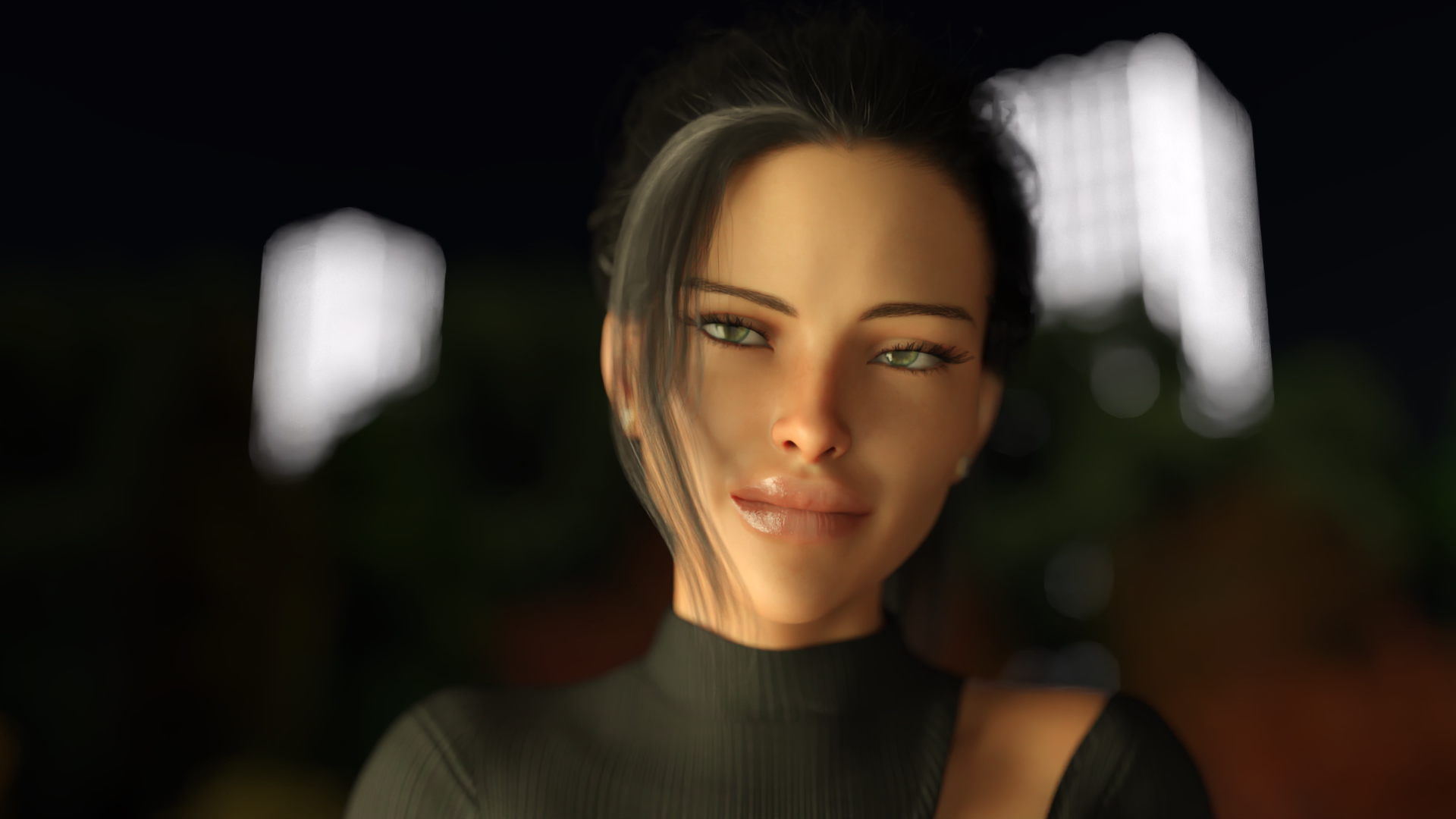
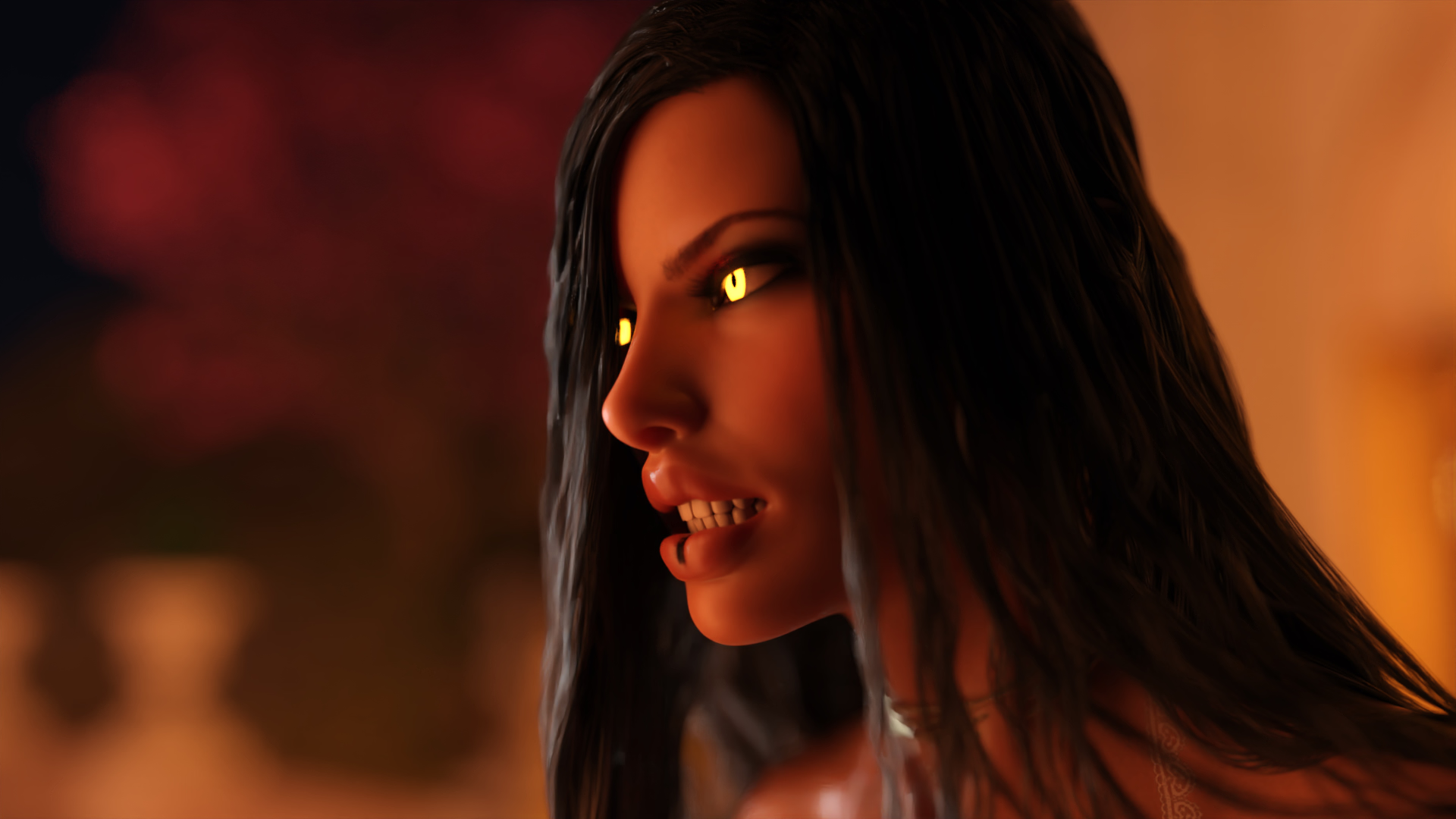
Detail Author:
- Name : Herta Legros
- Username : price.timmothy
- Email : monserrat.hermiston@yahoo.com
- Birthdate : 2004-05-27
- Address : 55953 Renner Island South Jacey, WI 18254-8317
- Phone : 406-326-2266
- Company : Cummings, Hintz and D'Amore
- Job : Aircraft Structure Assemblers
- Bio : Vel ipsa et odio qui sapiente unde. Sed dolores consectetur atque hic. Molestiae a aut sunt dolor ut. Perspiciatis sequi et minus maxime animi est magni.
Socials
instagram:
- url : https://instagram.com/wilson.armstrong
- username : wilson.armstrong
- bio : In voluptates autem et aut. Ut ut quibusdam tenetur. Et aliquam officiis velit nesciunt.
- followers : 5225
- following : 2944
twitter:
- url : https://twitter.com/warmstrong
- username : warmstrong
- bio : Nihil eaque reprehenderit nemo qui. Et omnis aut est sed quia ut. Ut impedit eos repellat vitae qui. Temporibus accusantium et vel saepe.
- followers : 1279
- following : 297
facebook:
- url : https://facebook.com/wilson.armstrong
- username : wilson.armstrong
- bio : Soluta omnis veritatis aspernatur quo velit explicabo.
- followers : 6270
- following : 643